Latest News

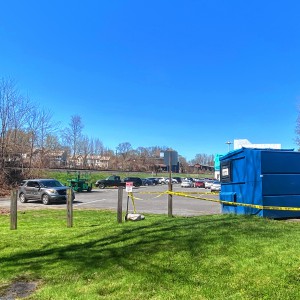
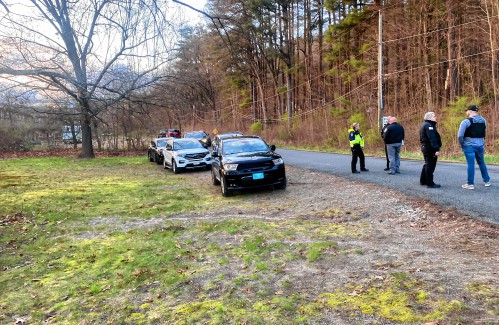
Police report details grisly crime scene in Greenfield
SUNDERLAND — Police located a cabin in the woods around Clark Mountain Road Thursday afternoon believed to belong to Taaniel Herberger-Brown, the suspect accused of murdering a man at 92 Chapman St. and storing his body in a plastic barrel for an...
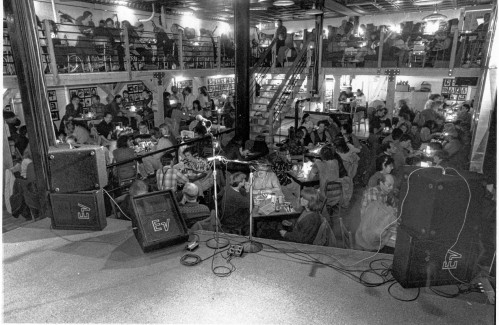
The Iron Horse rides again: The storied Northampton club will reopen at last, May 15
In late March, the fabled Iron Horse Music Hall, slated to reopen in mid May, was still a pretty raw construction site.Boards, pipes, boxes, and other materials were piled on the floors, along the walls, and on tables. Extension cords to power saws...
Most Read
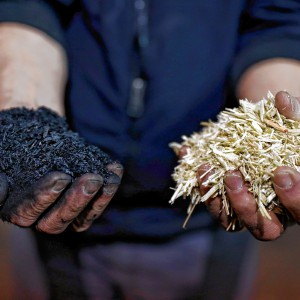
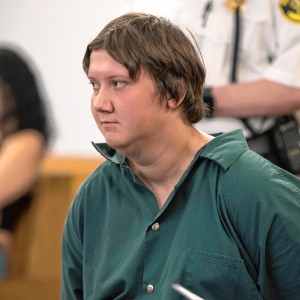
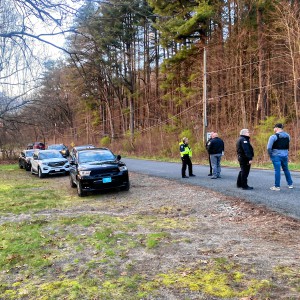
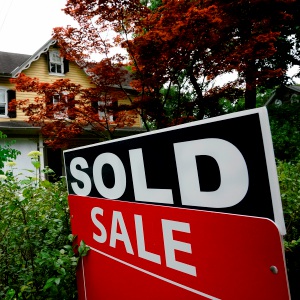
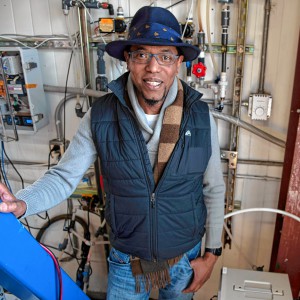
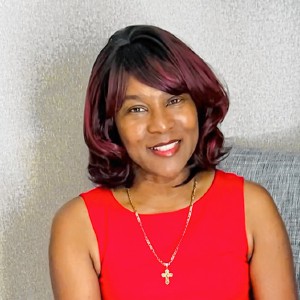
Editors Picks
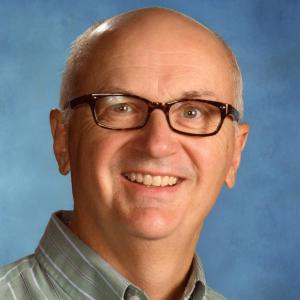
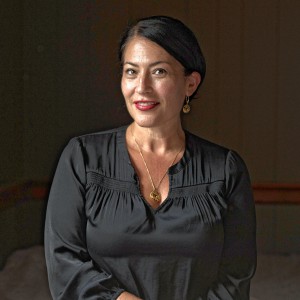
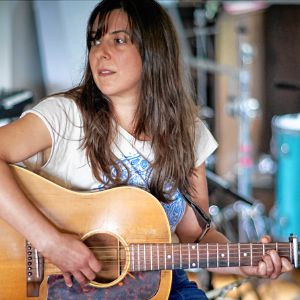
Sports
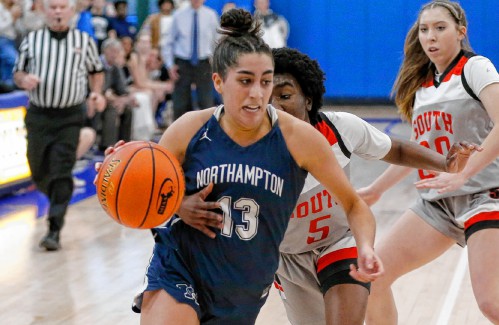
2024 Gazette Girls Basketball Player of the Year: Ava Azzaro, Northampton
NORTHAMPTON — Staring a six-point deficit square in the face in the fourth quarter of the MIAA Division 2 girls basketball quarterfinals, Northampton senior captain Ava Azzaro wasn’t ready to call it quits on her high school career.The No. 7 Blue...
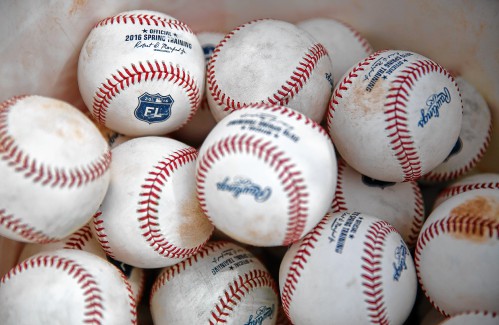
Opinion
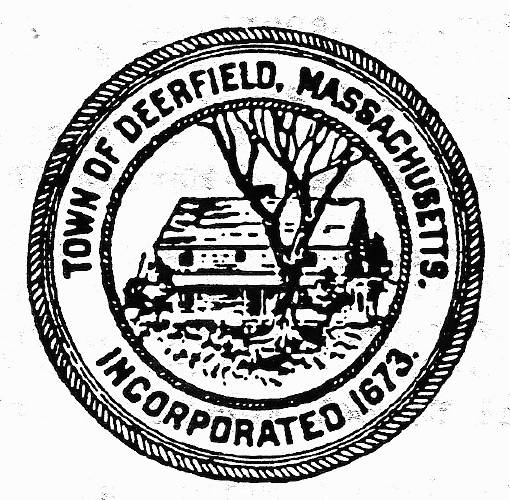
Charlene Galenski: Blake Gilmore, a strong candidate for Deerfield’s Selectboard
On May 6, Deerfield will have its annual election for local positions. Blake Gilmore is running as a candidate for Selectboard. Deerfield is facing some financially challenging times. Over the past few years, the town has voted to finance several...
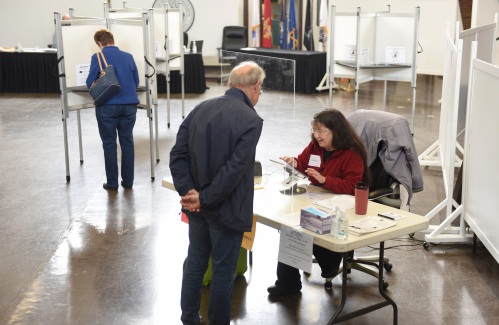
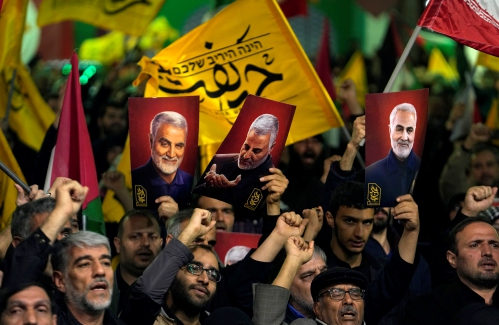
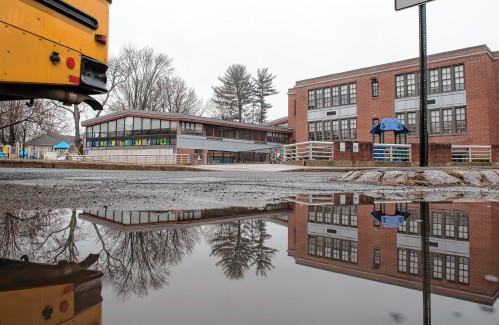
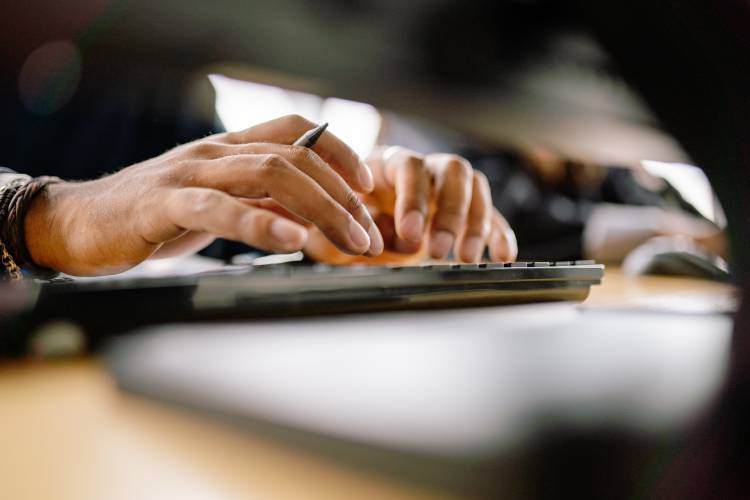

Business
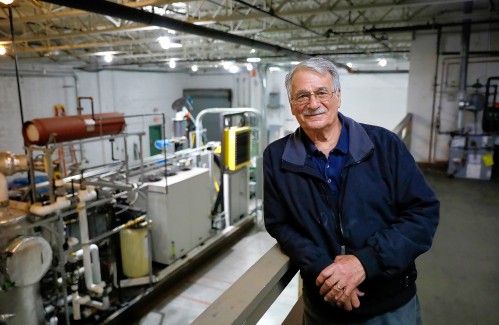
Locking up carbon for good: Easthampton inventor’s CO2 removal system turns biomass into biochar
HOLYOKE — Like many people, Michael Garjian believes global warming is a pressing issue of our times.Unlike most, he’s putting his ideas for reducing carbon dioxide in the atmosphere into practice — and at the same time bidding for a share of the $100...
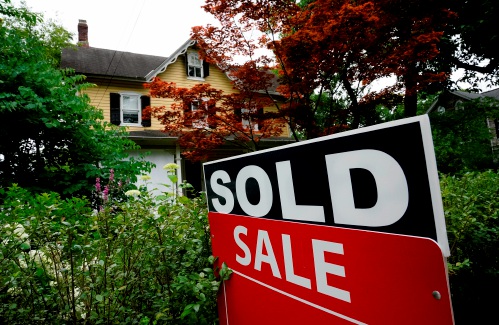
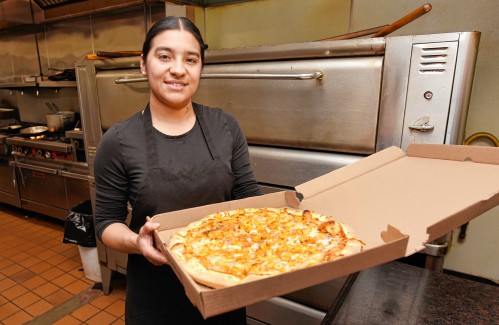
Arts & Life
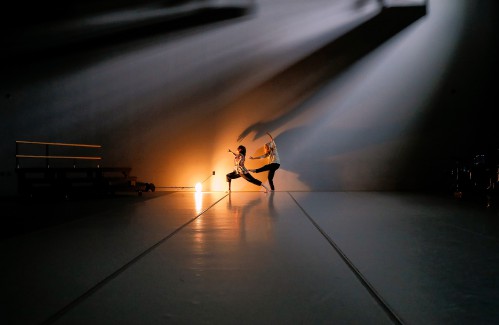
Upon Nancy’s Floor: 33 Hawley event celebrates iconic dancers, history, and a new dance floor
Among the many features that are part of 33 Hawley, the Northampton Community Arts Trust building that was finally completed in early January following 10 years of construction, there’s probably nothing more important to dancers than the floor of the...
Obituaries
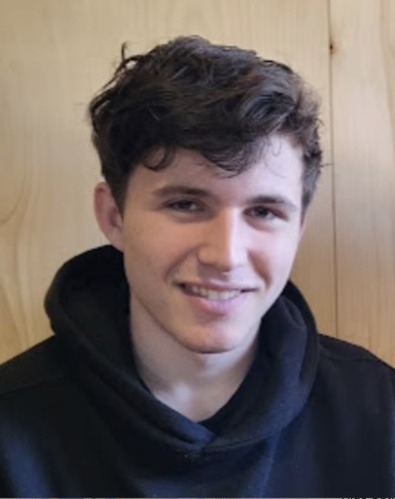
Florence, MA - Eli Knapp Abrams, of Florence Massachusetts, passed away suddenly on Monday, April 22nd, 2024 in Goshen, MA. Eli was born in Beverly, MA on March 19th, 2003. He is the cherished son of Jennifer and Maury Abrams, and belov... remainder of obit for Eli Knapp Abrams

Plymouth, MA - Pat, wife, mother, and grandmother, passed away on Saturday, April 20th after a long battle with cancer. Daughter of Valerian and Regina Latka, she leaves behind William, her husband of 54 years, her son Kevin and his par... remainder of obit for Patricia Taylor
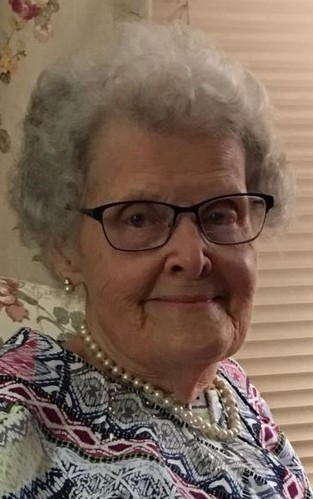
Greenfield, MA - Audrey A. McKemmie of Greenfield and formerly of Amherst passed away on April 23, 2024, after a period of declining health. Born in Greenfield, December 12, 1930, she was the only child of John and Susie (Hayden) Kolink... remainder of obit for Audrey McKemmie

South Hadley, MA - South Hadley Donald E. Hooton, 91, passed away peacefully on Sunday, April 21 st , 2024, surrounded by his loving family. He was born in Holyoke to the late Eva (Utley) and Leonard Hooton. Donald moved to South ... remainder of obit for Donald E. Hooton